Transforming Energy for America
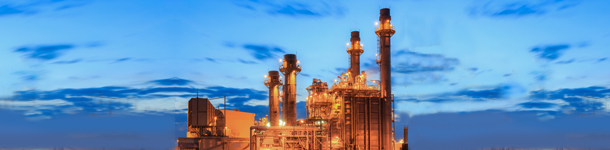
ENERGY AND EPC
Virginia Transformer Corporation has a special focus on the Energy Generation and EPC market sectors.
Consistent growth and the addition of the Georgia Transformer facility specialized for large power allows us to offer the energy and EPC sectors a complete portfolio from small power up to large GSU and auto-transformers. We also provide complex multi-tap changer transformers used for station service applications.
Our state-of-the-art manufacturing facilities in Virginia, Georgia, Idaho, and Mexico have a strategic advantage to build custom transformers and service sites all over North America.
We are well supported by a dedicated, experienced, and professional sales representative network that works with our dedicated sales team. We are always here to help!
Our team is educated in serving some of the biggest electrical power producers in the world; with clients specialized in sectors ranging from fossil fuel to renewable and nuclear energy utilization. We understand what success looks like in each of these unique environments and have the expertise to serve.
High project visibility with EPC (Engineering, Procurement and Construction) customers means that selecting us as your partner that will give you the advantage of a solid track record winning projects that is a critical first step. Our solid track record of winning projects is because of our unparalleled service that is specially oriented toward execution of reliable on-time deliverables.
We are one of the few companies that completely designs, manufactures, tests, and supports field installation from each of our factories. With a dedicated engineering staff who designs, check, and follow each project from inception to completion and that ensures the conceptual design is the same and the final product. Additionally, each of the factories are ISO 9001-2015 certified. This along with a rigorous inspection team verifying and validating that the processes are being adhered to help provide a quality product that will provide many years of trouble-free service.
During the process, each project is assigned a project manager that will work with the end user to provide day-to-day progress reports as needed. This person will be the prime contact point from the beginning of the order starting with our “kick-off meeting” continuing up to the time of shipment. This one point of contact will provide regular and consistent communication with each of our customers so that we can keep them up to date with progress.
Each of our factories have new core cutting machines that can provide a product that has a burr limit of less than 20 Microns and manufacturing step lap core utilizing the highest grades of grain-oriented core steel. This enables us to provide extremely low core losses and reduce the noise of the transformer. We also utilize vapor phase drying in both the core and coil in our factories to ensure that the final product is fully dried prior to final sizing. All factories are equipped with the necessary equipment to fully test every transformer per IEEE-C57.12.90-2010 with annual certifications on all equipment and certified test reports for all equipment provided.