DRY-TYPES TRANSFORMERS
Overview
The 1970s were the formative years for Virginia Transformer, where our product offering was primarily specialty harmonic load transformers. In the 1980s, we invested in industrial solutions for mills, transit, and rail. By the 1990s, we diversified to utility generation, transmission, and distribution. In the 21st century, we added large power transformer capability to our portfolio to support the renewable energy generation sector where we currently hold the largest market share.
Virginia Transformer takes pride in being a U.S.-based
power transformer OEM with the mission to single-handedly reduce US power transformer imports and bring power transformer manufacturing jobs back to the U.S. To support our mission, we expanded our manufacturing capacity by adding 6 additional plants while also adding management and technical resources in the U.S., Mexico, and India.
We have established strategic sourcing partnerships
with vendors in the U.S., India, and China to ensure a
robust supply chain.
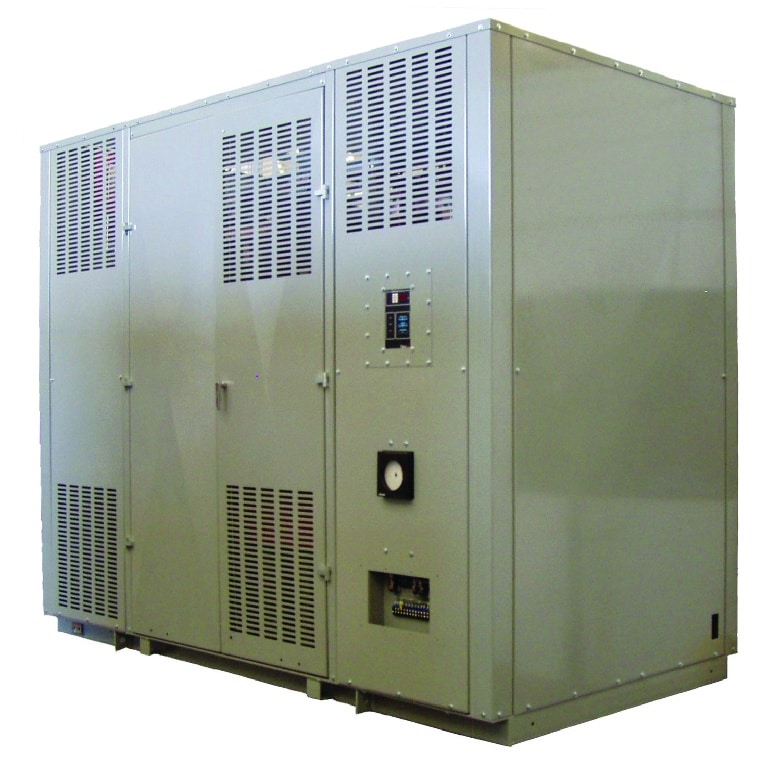
VTC’s Dry-Type Transformers
Virginia Transformer first began producing dry-type transformers in the 1970s. Over the years, we have refined our design and technology, enabling us to manufacture dry-type transformers from 300 kVA to 20 MVA, up to 35 kV class. Applications for dry-type transformers include commercial buildings, airports, hotels, industrial plants, mines, and data centers. Virginia Transformer’s dry-type units are built to withstand the toughest environments. We use aluminum conductors, temperature-controlled winding rooms, superior insulation, and special harmonics handling to produce reliable transformers with the lowest core losses.
- Shortest lead times
- Proven technology since 1971
- Designs for any industrial and commercial application
- Choice of coil processing
- Enclosure for indoor or outdoor applications
- Units designed for high-humidity or corrosive environments
- UNIClad - a premium dry-type transformer exclusively from Virginia Transformer
TRANSFORMER FEATURES
RANGE
- Up to 15/20 MVA
- 35 kV voltage class
- 150 kV BIL
LOADING
- Designed to deliver rated current and MVA in all tap positions
SERVICE
- Outdoor or indoor
BASIC IMPULSE LEVEL (BIL)
- Per ANSI standard
COILS
- Aluminum or copper conductor
- Circular or rectangular construction
- Disc or barrel wound
COIL SEALING
- Vacuum Pressure Impregnated (VPI)
INSULATION
- 220 ºC insulation system
ENCLOSURE
- NEMA 101/103R
- Complete breakdown crowned roof for water shedding base suitable for lifting
- Jacking and skidding
PAINT
- ANSI 61 enamel on phosphatide cleansed surface
NAMEPLATE
- Engraved stainless steel for outdoor use
- Metallized mylar adhesive for indoor application
4 PAINT SYSTEMS AVAILABLE
- The application engineers at our National Sales Office will offer assistance in assuring the best process and enclosure for your application
STAINLESS STEEL GROUND PADS
12 – 18 month standard warranty options:
- Electronic temperature monitor
- Load break switches
- Matching to all OEM switchgears
- Drive/rectifier duty up to 36 pulse
OTHER TYPICAL APPLICATIONS INCLUDING MAIN USE IN DATA CENTERS
- Subway
- Rapid transit
- Hospitals
- Hotels
- Schools
- Utilities & power plants
- Chemical Plants
- Mining operations
- Paper & steel mills
- Oil & gas refineries
- Office & shopping complexes
- Manufacturing plants
- Airport terminals
- Water treatment plants
- Research facilities
MARKETS
- Switchgear – Siemens, Cutler Hammer, Square D, GE
- Transit – NYCTA, WMATA, DART, LIR, LA Metro, San Diego Metro, Houston Metro, RTD (Denver)
- Metals – US Steel, Nucor Steel, ALCOA, California Steel, N American Stainless, IPSCO Steel
- Chemical – PPG Industries, Dominion Cove Point, DH Compounding, Occidental Chemical
- Government – US Dept of Energy, NASA, US Navy, IRS, Fermi Lab
APPLICABLE STANDARDS
- ANSI - American National Standards Institute
- IEEE - Institute of Electrical and Electronic Engineers
- C57.12.01 - General requirements for dry-type transformers
- C57.12.51- Requirements for ventilated dry-type power transformers 501 kVA and larger, three phase, with high voltage 601 to 34,500 volts, low voltage 208Y/120 to 4160 volts
- C57.12.52 - Requirements for sealed dry-type power transformers 501 kVA and larger, three phase, with high voltage 601 to 34,500 volts, low voltage 208Y/120 to 4160 volts
- C57.12.91 - Test code for dry-type distribution and power transformers
- C57.94 - Practice for installation, application, operation, and maintenance of dry-type general purpose distribution and power transformers
- C57.96 - Guide for loading dry-type distribution and power transformers
Processing for Coil Protection
VPI: The coils are dried and then sealed with thermoset polyester varnish under vacuum conditions. The process requires proprietary processing of vacuum temperature and pressure, and results in a completely sealed coil.
COIL OPTIONS
SHAPE
- Rectangular
- Circular
WINDING
- Barrel
- Disc
CONFIGURATIONS
- Delta-Wye
- Zig-Zag
- Wye-Wye
- Delta-Delta
- Phase Shifters
SEALING
- Polyester varnish VPI
- VPI and epoxy end caps
- Unidip
- UNIClad®
CONDUCTORS
- Aluminum
- Copper
ENCLOSURES
NEMA 101: Clean indoor applications
NEMA 103R: Outdoor applications per ANSI standards C57.12.55
NEMA 103 R: Coastal Applications per ANSI Standard C57.12.59
TENV: Totally Enclosed Non Ventilated – Indoor/outdoor application where corrosive gasses, high dust, and other contaminants are present
TOTAL COIL TEMPERATURE
Average Temp. Rise by Resistance | 150°C | 115°C |
Ambient Temp. (Maximum) | 40°C | 40°C |
Hotspot Temp. Allowance (est.) | 30°C | 30°C |
Total Temp. of Coil | 220°C | 185°C |
Unidip Processing for Dry-Type Transformers
- The environment contains medium levels of moisture or inorganic particles and gasses produced in manufacturing.
- The load variation is wide and frequent.
- Regular equipment servicing is not possible.
The Process
- Coils are wound with insulation processed in a controlled environment to reduce moisture content to a minimum.
- Finished coils are dried in a hot-air oven above 230ºF.
- Hot coils are placed in a vacuum chamber at less than 15 Torr (mm of mercury absolute pressure) to remove all remaining moisture and gasses. Water will vaporize at this pressure at less than 25ºC.
- Thermoset polyester (or other specified resin) is added under vacuum to cover the coils completely. Thermoset polyester is a 220ºC-rated resin when used with 100-percent solid insulation and no solvents.
- Coils are soaked in this resin to seal the insulation porosity against all industrial contamination and gasses to ensure full life of the insulation in actual service.
- Resin fills all voids in the coil to ensure a solid insulation system.
- Resin is pressed into the coil with greater than 5 atmosphere pressure (80 PSI) to ensure full penetration into the coil and insulation to make a solid coil consisting of conductor, insulation, and duct sticks.
- Resin is withdrawn from the chamber.
- The coil is placed in a preheated oven to cure the resin at the required temperature and time for a complete cure.
- The coils are assembled with the core. Connections are made to the HV and LV bus/cable; tap connections are made to the terminals/cable. The assembly is tested to verify design performance.
- The complete assembly is heated in a hot-air oven above 230ºF.
- The hot core and coil assembly complete with all wiring and bus connections are processed in a resin mixture containing thermoset polyester resin rated at 220ºC, inorganic filling compound rated for operation at greater than 1000ºC to assure a high continuous-use temperature, and an inorganic compound to provide a barrier against diffusion of water and other chemically similar molecules encountered in industrial processes and manufacturing.
- The hot assembly is covered with the resin-compound mixture in a vessel equipped to maintain the mixture ratios and allow for removal of excess resin to clear all cooling passages and ensure long life of the insulation system.
- The resin starts to cure and forms a thick (.005 Inch/ >125 microns) cover that seals all parts of the coil, connections, and the mechanical hardware to protect against vibration, shock, and rusting in industrial manufacturing environments.
- The resin is cured by placing the assembly in an air-circulating oven at the recommended temperature and time.
- The core and coil assembly is sealed against industrial gas, vapor, and moisture contamination.
- The insulation system is protected from the industrial environment and moisture to deliver full design life of more than 20 years when operated within the designed temperature and dielectric stresses.
- Unidip coating will withstand 95 percent relative humidity and subsequently pass all ANSI standard dielectric field tests.
- The mechanical system of the core and coil assembly is protected from loosening due to industrial vibrations and shocks.
- The mechanical parts of the core and coil assembly and the electrical connections will not rust in humidity encountered in industrial manufacturing.
Unidip-processed, dry-type transformers from Virginia Transformer Corp. of Roanoke, VA, USA, are equal to or better than cast resin or other sealed encapsulated dry-type transformers in their overall performance in the capital and consumer goods manufacturing environment. Additional environmental protection can be achieved by using optional accessories offered by VTC for long-term storage.
Unidip vs. Cast Oil – The Choice is Clear
VTC developed Unidip to operate under demanding
applications in harsh environments. Because it is designed to withstand industrial fumes and vapors, fibrous and particle contamination, high
temperature and humidity, short-circuit forces, and electrical voltage impulses, Unidip is the cost-effective alternative to liquid-filled or cast-coil transformers. Unidip is a perfect solution for power, rectifier, drive isolation and generator exciters up to 15,000 kVA, 35 kV class.
Desired Features | Unidip | Cast Coil |
---|---|---|
High thermal rating | Excellent: 220°C | Acceptable: 150°C to 185°C |
Overload capacity | Very Good: 15% overload without fans | Limited: fans necessary for overloading |
Seal integrity | Yes: flexible insulation and cladding system eliminates coil cracking | No: Coil cracking because of rigid casting and high thermal coefficient of epoxy expansion |
Void-free coil | Void density is low because of low varnish viscosity and vacuum/pressure process | Void density is higher because of high viscosity of epoxy resin |
Superior short-circuit test performance | Yes: performed with 0% impedance change in a 4-duration test, which is 60 times longer than required per ANSI standards | No: passes standard ANSI test of 4 tests of 4 cycles (60 Hz) each, with less than 2% impedance change |
High percent tensile | >20% | <5% |
Flexible designs | Yes: All Unidip units are designed to customer specifications | No: must choose from existing molds |
Design tested | Internal and external are self-extinguishing; vibration shock of 30G | Not available |
Quick delivery | Yes: typically 10 to 12 weeks | Limited: typically 12 months |
Competitive pricing | Yes: never need to upsize; Unidip units are designed exactly for customer's application | Sometimes: choosing from pre-set molds can result in a 10% to 15% premium, because any non-standard design may force customer to order larger-sized unit than they actually need |